World Class Installation and Support
On site installation and training with lifetime service and support is a standard component of our full solutions services. Our install team will get you up and running with your new coating system and get you started with process development tools to enable you to quickly optimize your coating processes.
We pride ourselves on providing world class service and support to our customers around the globe. We have an extensive network of distributors located in dozens of countries worldwide, including local language support. In addition, we have multiple laboratory locations available for atomization and process testing. Please contact us for information regarding distributors in your area.
Protect Your Investment with One of Our Service Plans
We highly recommend purchasing a spare parts package and an annual service plan in order to best protect your investment into a precision Sono-Tek coating system. We offer spare parts packages and service plans to fit all budgets. Our expertly trained Service staff will help keep your machine running effectively and efficiently for many years to come.
Three levels of Service Plans are available for most systems – Steel, Titanium, and Cobalt.
- All plans include a yearly on-site check-up and extended warranty on ultrasonic nozzle(s).
- Higher level plans offer quicker response time and discounts on service visits and repairs, ideal for production environments where downtime is critical.
- Spare parts packages are available as well, contact us for more details.
Direct Customer Support
Sono-Tek’s team of application engineers provide direct customer support throughout every step of the process.
Process Knowledge – Discuss and Spec In Coating Equipment
- 40 years of combined coating knowledge and expertise
- Thousands of coating trials
- Hundreds of chemistries tested
- 6 dedicated full time applications engineering team members
Lab Testing – Prove Concept
- In-house full testing laboratory with full array of available equipment, including SEM, precision measuring equipment, photosensitive lighting, protective fume hood, curing ovens
- Testing performed with or without customer present
- Initial proof of concept using customer materials and substrates whenever possible
Coating Services – Produce Coated Products
- In-house process development to meet customer’s goals
- Toll Coating services/small production run of established coating processes
- Small batch coated samples to fill immediate need while Sono-Tek system is being built to order
System Design – Personalized Build for Application
- Use all data and applications knowledge gained from prior steps to design and build the most effective coating solution
- Thousands of system configurations possible
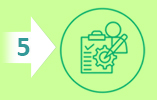
- Process guidance from application engineering experts for the lifetime of the system
- Process refinement and troubleshooting issues, with customer site visits available
- Support for future upgrades or system changes due to process alterations
In addition to the New York lab, Sono-Tek has applications labs located at distributor sites around the world; all of which are staffed with engineers who have experience working with customers on ultrasonic coating solutions.
Our global distribution network includes local language support for many countries. Select an icon on the map for location information.